Puppet - Roxy
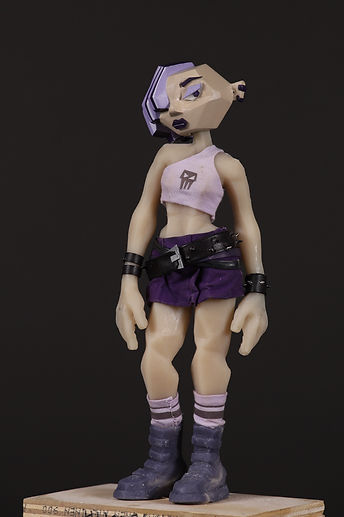
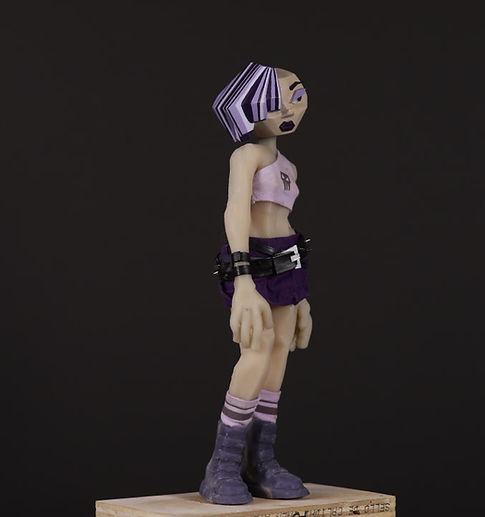
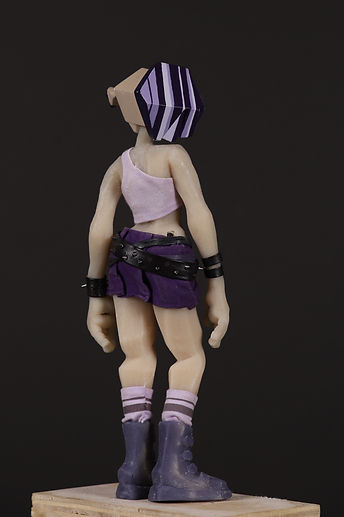
*Responsible for sculpting/molding, armature/rigging, silicone casting/cleanup, and head/expressions.
The head sculpt was started by Erika Totoro and then further developed by Dahlia Kressler. When I received it, I made adjustments to some of the underlying structure.
Polycarbonate Armature
Roxy's armature is constructed from 1/8" wire housed within polycarbonate pelvis block, which feature rigging ports drilled into the sides and back. The rigging includes two 10/24 ports on either side that are compatible with bolt-based rigging. She also has 4-40 ports on the front of her pelvis to allow a costume to be rigged to. Her chest block is sculpted in Propoxy and provides structure as well as a grab block for when animators are posing.
​
​


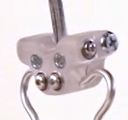

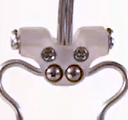

Knee caps were added to the armature in order to support the sculpted knee on the silicone, so that when the knee is bent, it retains a defined angular shape, making the posing look less rubbery.
Silicone Casting
Roxy was cast in degassed GI 1110 transparent silicone, with 10% activator and thinner. She features "paint-ins" on her feet for her large boots. The seam lines left by the casting process are buffed out with a soft bit at the end of a Dremel.


Puppet Repairs
The Roxy puppet experienced a few breaks during the course of production. Most notably the shoulder wire broke just above the chest block. Then the neck wire broke at the base of the neck, and finally the wrist wire broke just below the palm. I went through and fixed these breakages when they arouse along the different points in production.
Broken Shoulder:
The shoulder of the puppet had broken just above the chest block. To fix it, the back of the bicep had to be carefully cut open, and the broken 1/8" wire inside was removed. A 1/8" drill bit was then used to create a hole in the chest block, which was filled with 5-minute epoxy. Next, a new wire was inserted into the hole, and the edges were filled with fresh Propoxy. An aluminum tube, filled with 5-minute epoxy, was used to join the new arm wire to the unbroken wrist wire. Finally, the arm was sealed with silicone glue and closed back up.
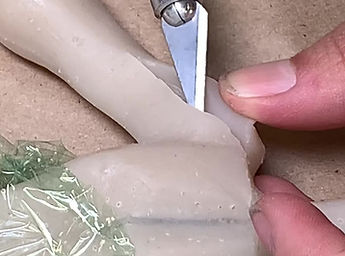




Broken Neck:
The wire had broken at the base of the neck on the puppet. The cleanest fix was to slice the body between the shoulder blades and follow a similar procedure to the broken shoulder. First, the old broken wire was cut off and sanded down. Then, a new hole was drilled directly behind the old neck wire and filled with 5-Minute Epoxy. The new wire was then fed through the neck into the back, straight into the new neck hole. Finally, the puppet was sealed up with silicone glue.

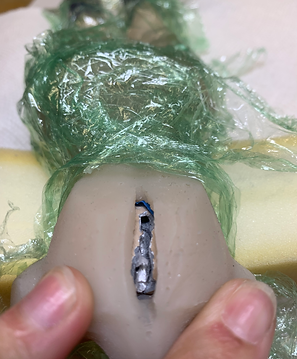
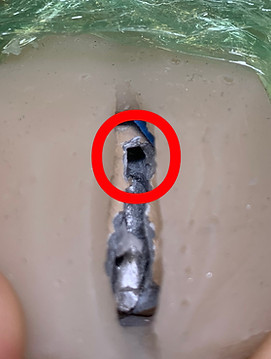

Head Fabrication
Roxy is a very geometric and graphic character. Her head went through lots of development and trial and error to get it into the best shape possible. Her expressions were equally graphic, so I generated and laser cut brows, eyes, pupils, lids, and mouths. After priming and painting the head, the eyes and mouths were added on top to create a cohesively stylized head for the character.
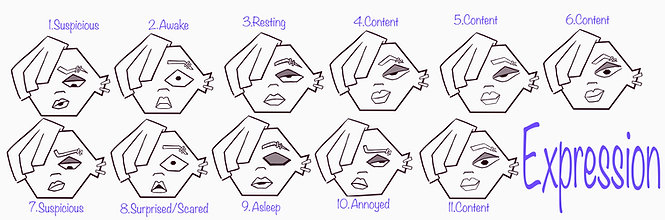
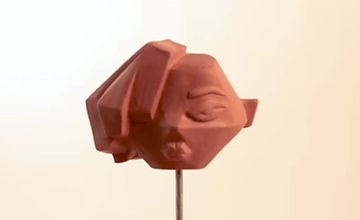
Expression sheet was created by Ami Aminatou.


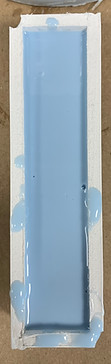

After creating a mold and cast for the head, more feedback was given late into production to add even more dimension to the facial structure. I sculpted Propoxy onto the face and chiseled and carved more structure and dimension into it.
I created these digital designs for Roxy's expressions based on the director's creative vision. The mouth was abstracted to its simplest silhouette while still being instantly recognizable, and then laser cut from 1/16th acrylic. A similar approach was used for the eyes, but they had to be fabricated in three different layers to ensure they were animatable. The whites of the eyes form the base layer, the pupils make up the middle layer, and the lids are the top layer.
The final head had a new mold made of it and then was primed and painted.
While the eyes and mouths were both laser cut from 1/16th acrylic, the mouths required a bit more dimension. So, I sculpted some three-dimensional shaping to the lips. After building a corral of foamcore walls, I poured activated G1000 silicone into it to create a silicone mold of the mouths. This allowed for easy replication of the mouths at a consistent and dependable level.
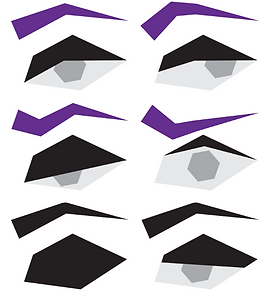
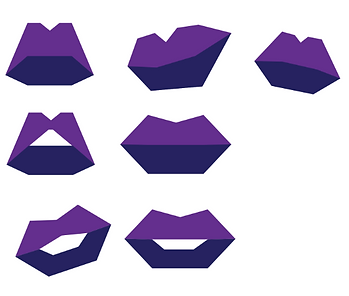
